WHAT LARCH TIMBER CAN WE OFFER YOU?
VISUALLY APPEALING MATERIAL
Larch is a scenic wood material. The cell structure of larch is precise and different from other tree species. Larch does not absorb moisture in the same way as, for example, pine. Larch is very resistant to mechanical wear and tear. A characteristic feature of larch is the strongly developed differences between winter and summer growths. In the core of the trunk, the reddish brown wood alternates with light brown, giving larch a unique visual structure that will caress the eyes of any lover of natural materials. When larch is exposed to the weather, it turns grey over time and changes its structure minimally over a long period of time.
Therefore, larch lumber is suitable as a cladding, not only for wooden buildings. You can use it in houses built with literally any building material. For example, because larch timber boards are attached to the house using a load-bearing grid, a ventilated gap is created between the timber cladding and the building itself. This makes a ventilated facade a safe solution for both masonry and timber houses, because even if there is an increase in humidity somewhere in the wall, it can evaporate from the building through the ventilated gap.
We will cut the larch boards for the facade according to your requirements quickly and cheaply. We buy larch raw material from the surrounding forests, so we can offer you a price that will pleasantly surprise you…
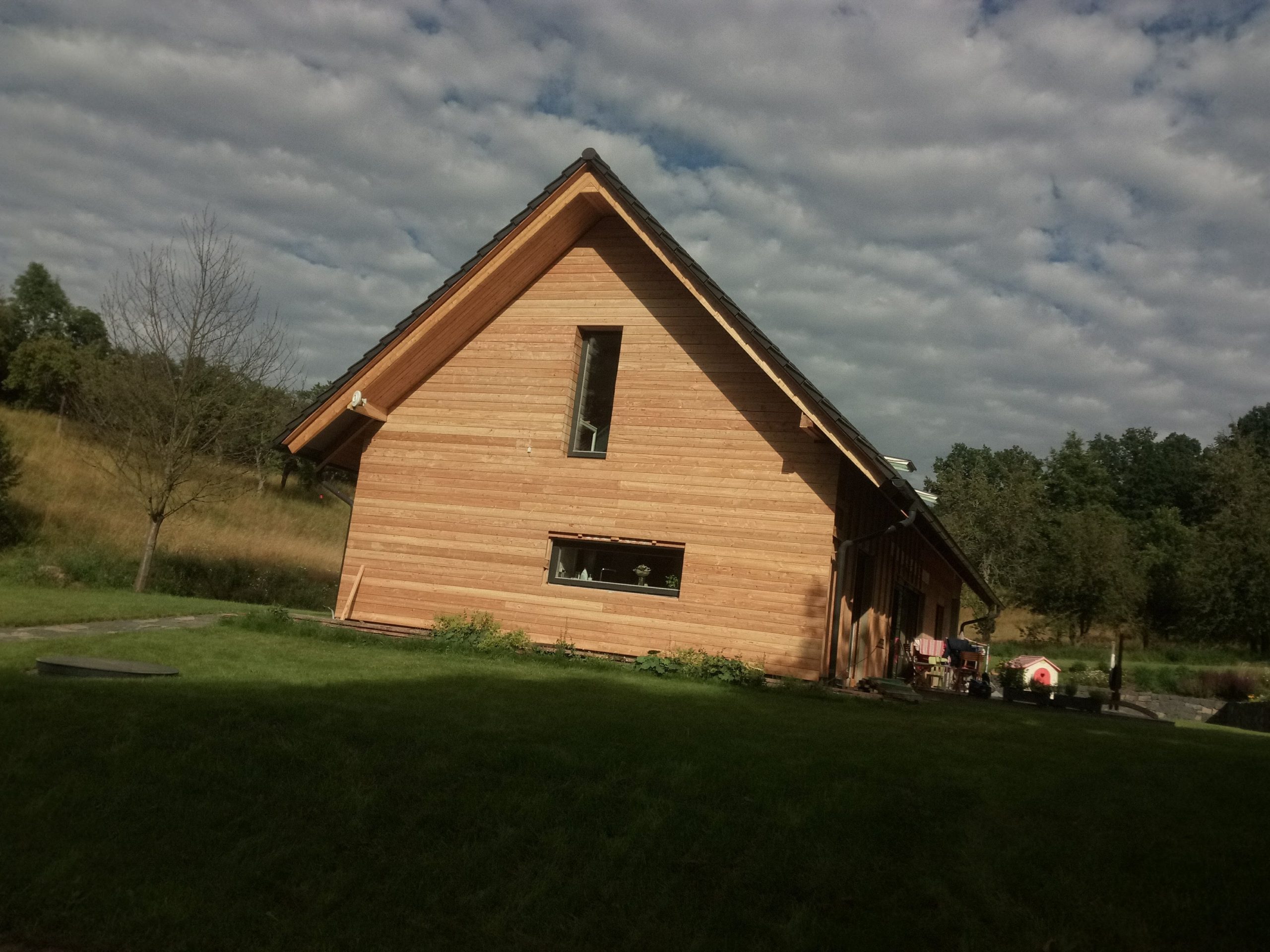
We specialize in the processing of larch. It is mainly larch lumber – both undried and dried semi-finished products for the production of solid floors, facades, terraces or decking. We also produce larch timber – battens, planks, beams, prisms, beams
Larch timber for planing is supplied in sawn thicknesses of 24mm, 29mm, 31mm, 34mm, 51mm, widths of 120mm, 158mm and lengths of 3000-5000mm in mixed ABC quality.
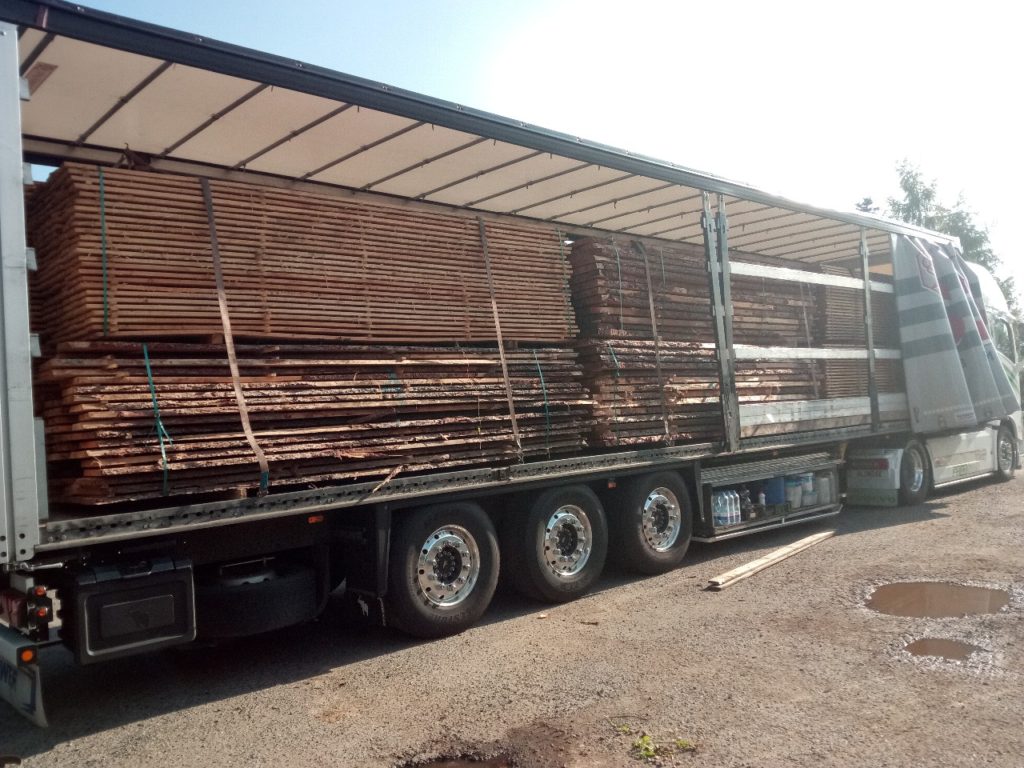
FEATURES
Slower growth than other conifers results in narrow annual rings with a distance between rings of only between 1-1.5 mm. In addition, there is a clear distinction between heartwood and sapwood and the proportion of heartwood can often be more than 90%. Heartwood is inherently durable and European larch wood is therefore often used as a substitute for pressure-impregnated wood.
Larch is left-handed throughout its growth, unlike spruce and pine, which are first left-handed and then right-handed. This means that larch twists more, which places greater demands on the fixing of the larch facade.
The knots are black-brown and pockets of resin may appear in the wood.
PROCESSING AND PROTECTION
Due to its high proportion of heartwood, larch has a greater durability than pine and spruce, without achieving the same durability as pressure-impregnated pine. This is particularly pronounced where the timber is in direct contact with soil or brick/concrete. In these areas, pressure-impregnated wood must be used to achieve acceptable durability.
Larch can be pressure impregnated and this should always be done if the timber will be in direct contact with soil or brick/concrete. However, pressure impregnation is only in the outer sapwood and therefore the protective effect is limited.
All timber must be protected as much as possible by ‘structural protection’, which means that you plan and build so that the timber is ventilated and water is drained away so that the material can dry out.
Wood is a natural material and will eventually turn grey. It is a good idea to protect the wood in dry conditions with suitable wood preservatives – either varnish or transparent wood preservatives. However, it is important to know that larch facades are difficult to treat with water-based wood preservatives.
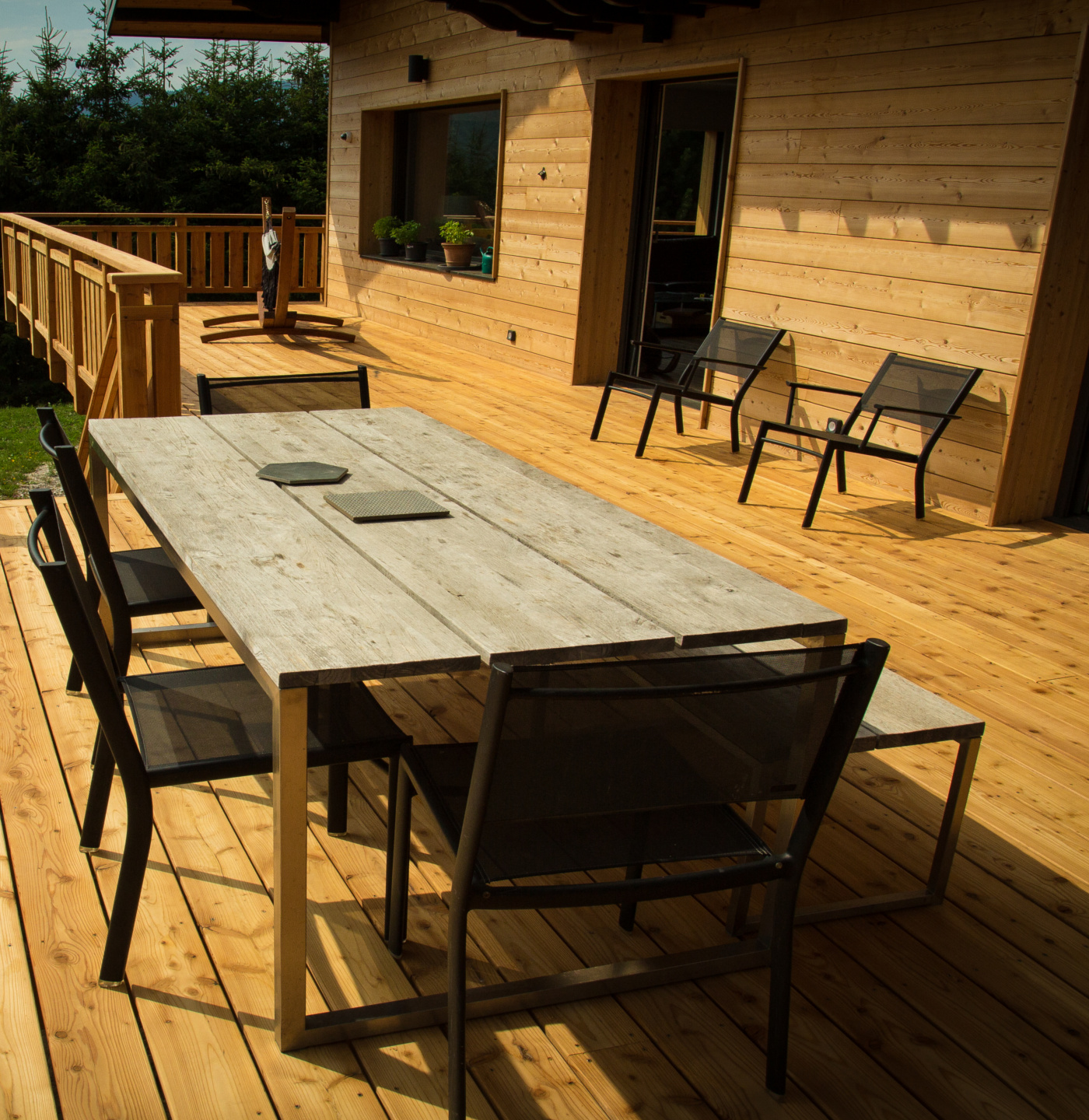
WHICH LARCH TIMBER CAN WE MAKE FOR YOU?
Freshly sawn (tarred) larch sawn timber with unspecified moisture content
The disadvantage of using unprocessed lumber may be the high water content and the subsequent volume changes and deformation when drying to equilibrium moisture content. The higher water content may also be problematic in terms of increased risk of attack by wood-boring insects, moulds and fungi, but this is to a small extent in oak, as larch is resistant to such attack.
When buying raw lumber, it is a good idea to choose the right quality for the application. In general, centre sawn timber, ideally radial with no pith content, will be the strongest and most stable.
On the other hand, the incorporation of elements made of uncured wood containing pith can cause undesirable effects in the form of twisting, drying cracks, etc.
This product of basic sawmill processing does not lose its popularity in traditional carpentry constructions, where a relatively wide range of cross-section dimensions is applied – exterior constructions, larch planks in the garden, raised beds and other
We’ll be happy to advise you on the selection of suitable material…
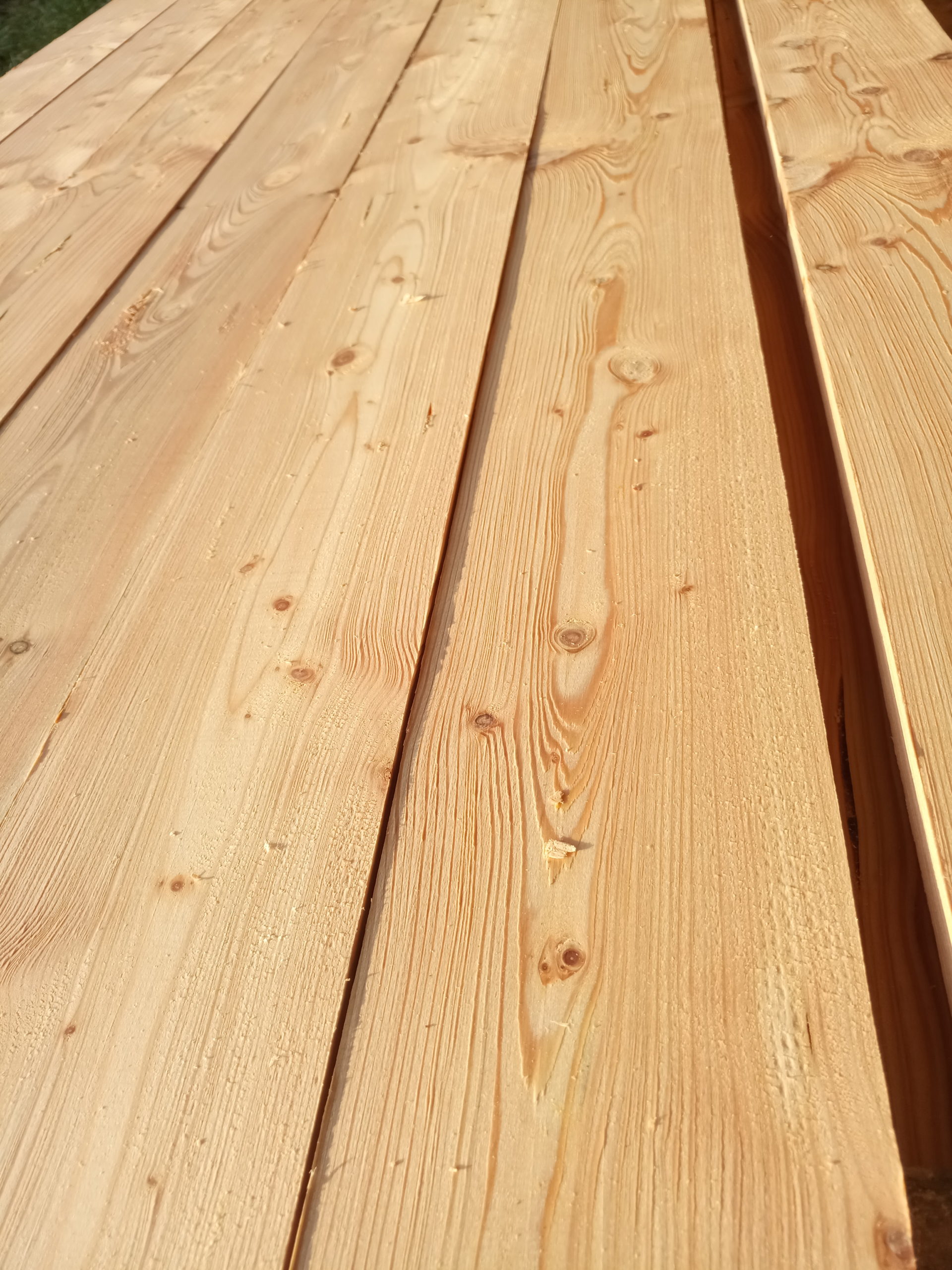
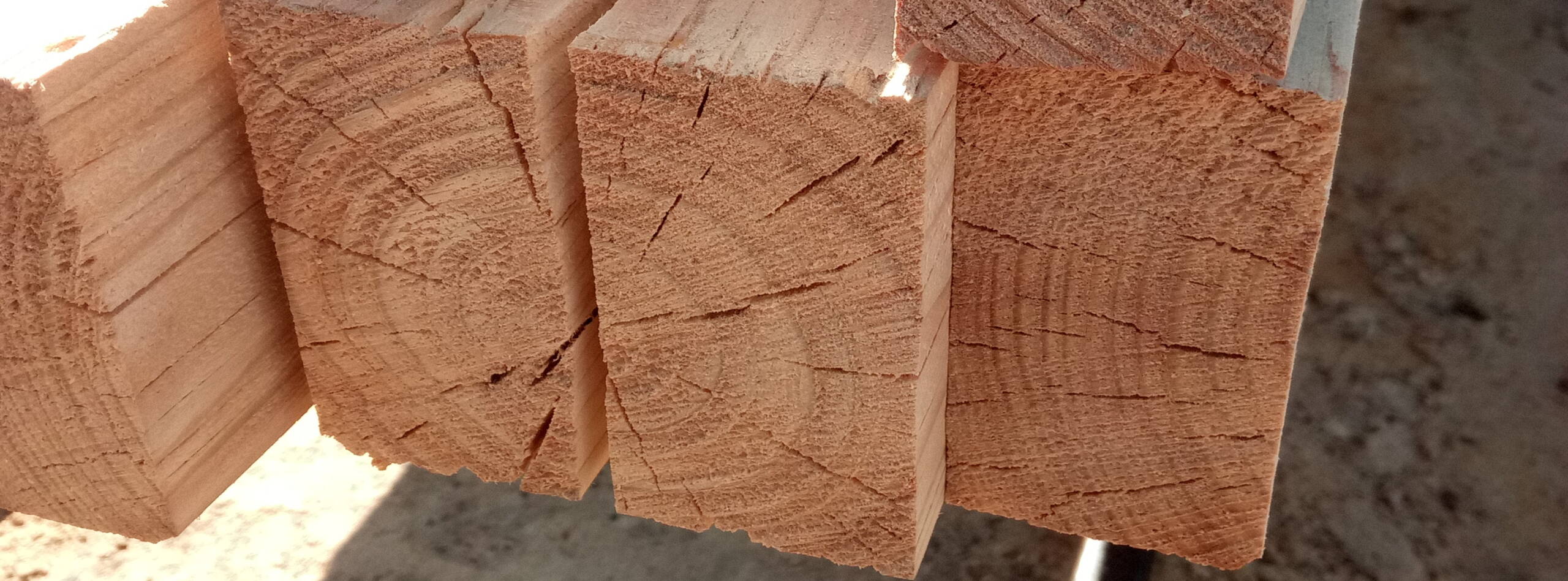
Technically dried, planed larch timber
The profiles are made of technically dried larch lumber with guaranteed moisture content (exterior usually 15% ±3%, interior 10% ±2%). The central lumber, ideally radial without pith content, will be the strongest and most stable, and care is taken to cut the pith (centre of the log) during the primary cutting of the log. This ensures greater dimensional stability.
Four-sided planing or sanding and chamfered edges are a matter of course for self-dried boards, battens, planks or beams.
For the production of larch lumber, logs are used in the order of the first and second pieces from the bottom of the tree with fewer cut branches (knots) and minimal curvature.
We’ll be happy to advise you on the selection of suitable material…
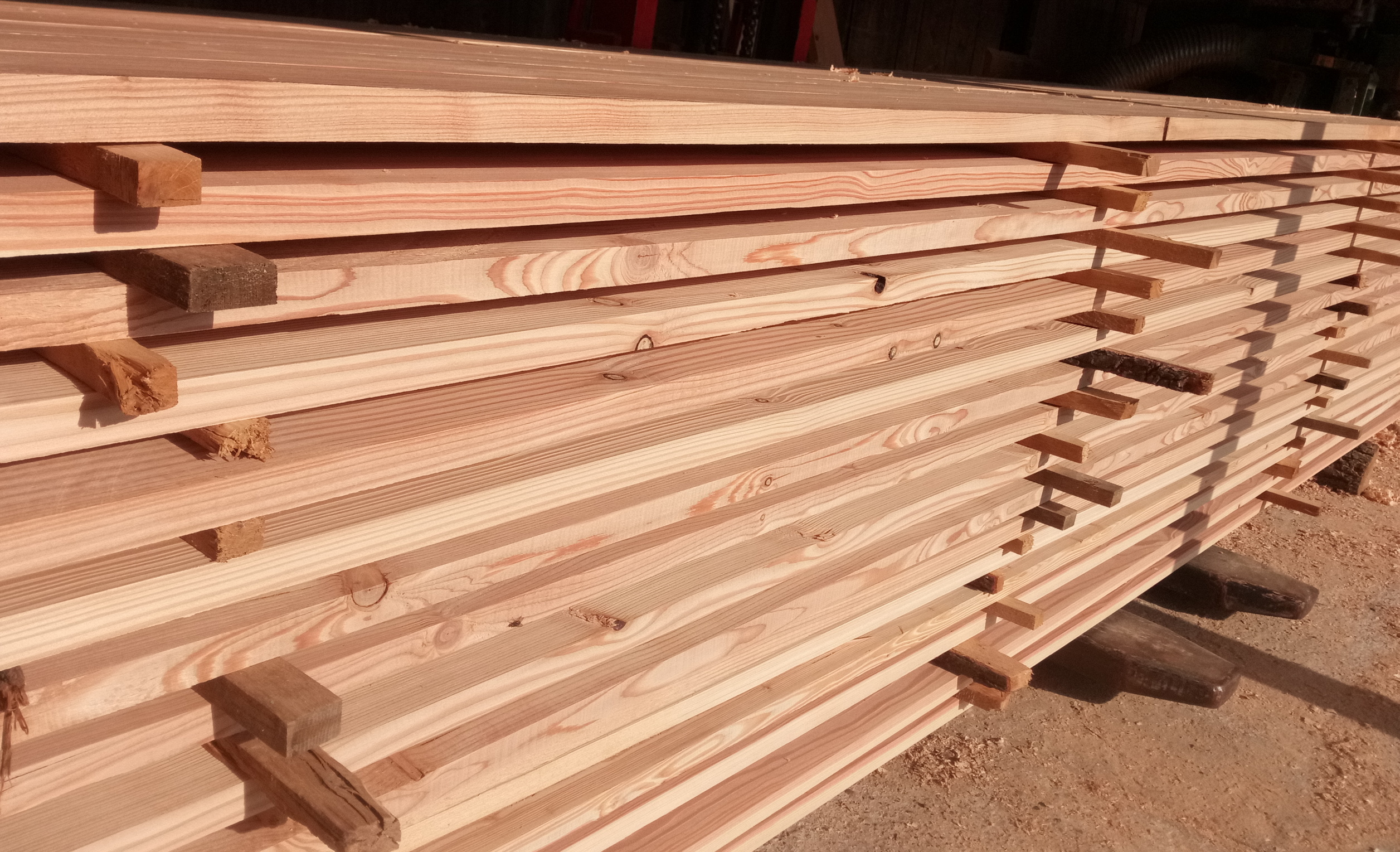
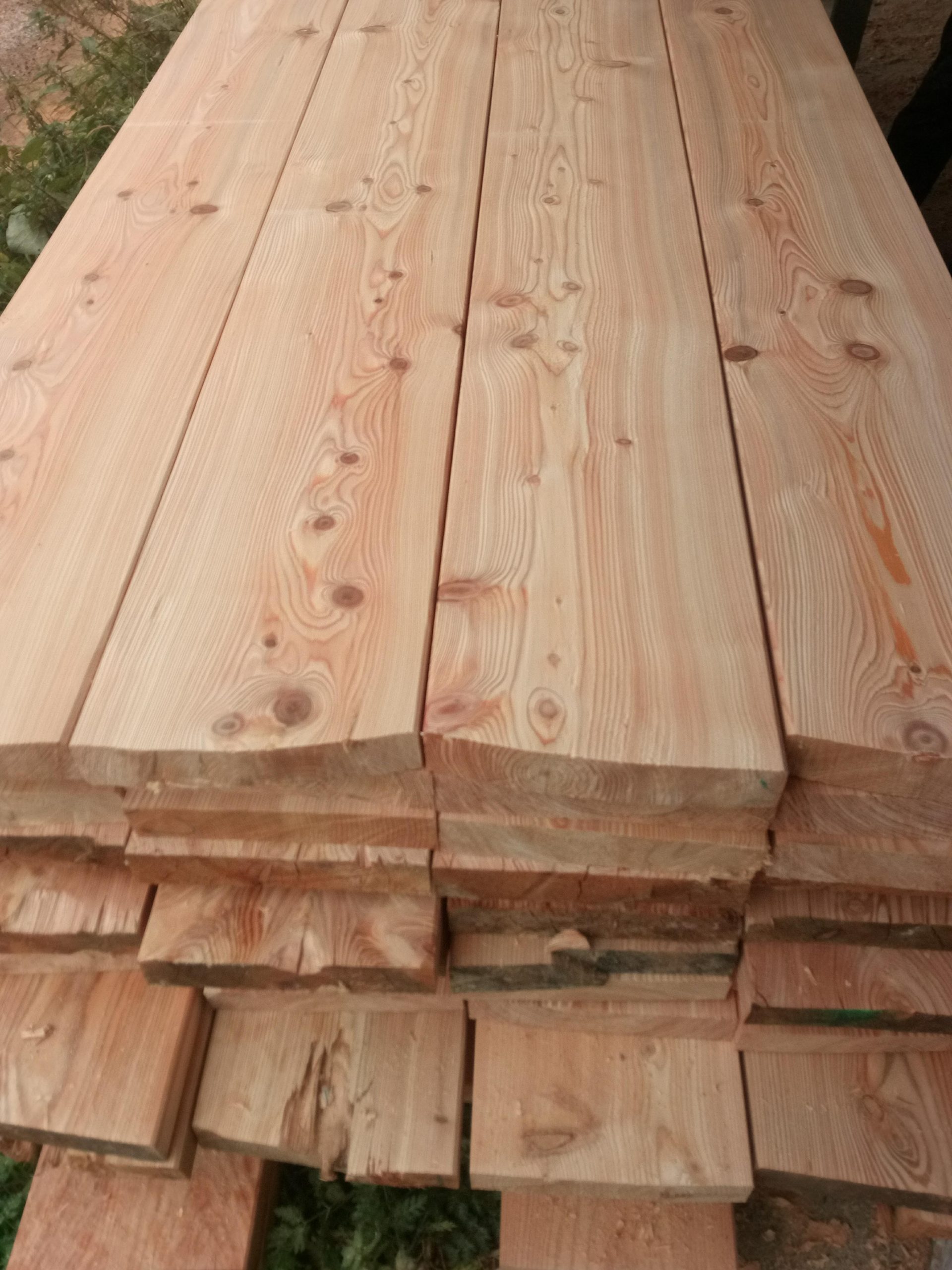
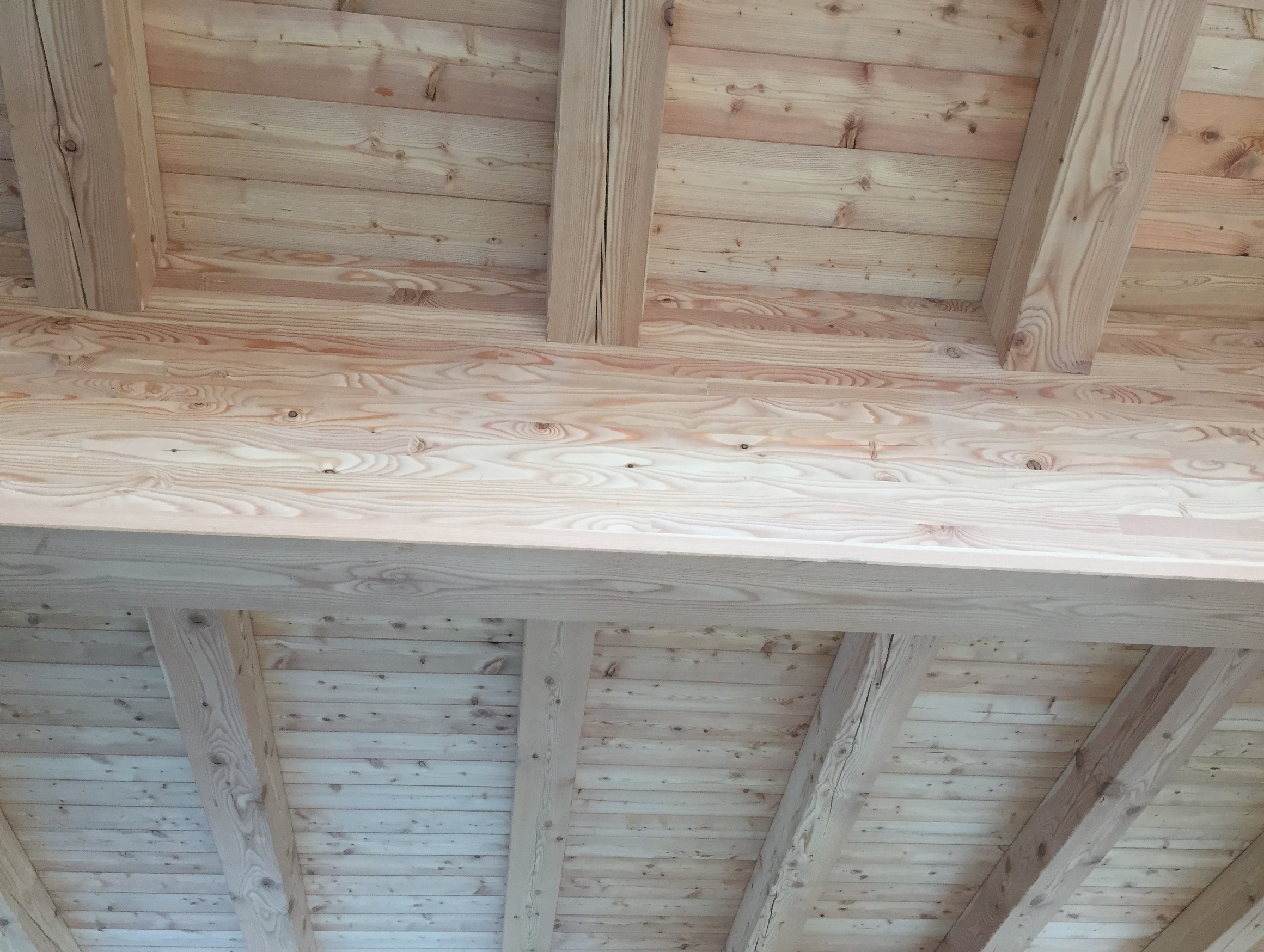
WHERE IS LARCH TIMBER USED?
Larch lumber is widely used in various areas of construction and gardening due to its exceptional properties. Here are the main applications of larch wood:
Building construction
Trusses and ceiling beams : Larch wood is popular for making wooden trusses and ceiling beams due to its strength and resistance to moisture
Pergolas and gazebos : It is ideal for the construction of outdoor structures such as pergolas and gazebos, where the emphasis is on both aesthetics and durability
Fences and garden furniture : Larch is often used to make fences and garden furniture because its natural properties repel water and protect the wood from fungi.
Outdoor floors and terraces
Decks and Floors : Larch decking is popular for outdoor decks and floors as it resists moisture and extreme weather conditions.
Facades and cladding
Building cladding : Due to its weather resistance, larch wood is often used for building cladding and facades, increasing aesthetic appearance and durability
Furniture
Quality furniture : Larch wood is also sought after for making quality furniture that combines beauty with functionality.
Ecological properties
Larch is considered an environmentally safe material, the use of which does not pose a threat to human health. In addition, the resin content in larch contributes to its resistance to mold and insects.
Thanks to these properties, larch lumber is in great demand both in the Czech Republic and on the international market, especially in areas with high requirements for wood resistance to weathering.
SPECIFICATIONS FOR CONSTRUCTION USE OF LARCH?
Larch, especially Siberian larch, is a highly valued material in the construction industry due to its unique properties. Its uses range from exterior structures to interior applications. Here are the key properties and specifications of larch for structural use.
Properties of larch
Durability and resistance : Larch is known for its high durability and resistance to moisture and rot. Thanks to the presence of natural oils and resins, it is able to withstand weathering, making it ideal for outdoor applications such as terraces, facades and wooden structures.
Strength and stability : Larch wood has high strength, making it an excellent choice for load-bearing structures such as beams and roof battens. Its structure with narrow annual rings (1-1.5 mm) contributes to its mechanical resistance
Aesthetics : Larch has an attractive appearance with a distinctive golden hue and distinctive grain pattern, making it a popular material for architectural applications.
Use in construction
Structural elements : Larch is commonly used for roof battens, beams, floors and cladding. Its properties allow for a wide range of applications including timber frame construction and ancillary spaces.
Exterior applications : Siberian larch wood is dried to an optimal moisture content of 18% ± 2% for exterior use, ensuring its acclimatization and long life in harsh conditions
Special applications : Larch is also used in shipbuilding and aircraft construction due to its combination of strength and lightness. It is ideal for the construction of sea piers, bridges and other engineering projects.
Processing and maintenance
Processing : Larch lumber can be supplied in various thicknesses (for example, 24 mm to 51 mm) and widths (120 mm to 158 mm), allowing flexibility in material selection for specific projects
Maintenance : Although larch is naturally resistant to moisture, regular surface maintenance is recommended to maintain its aesthetics and functionality. When used in areas with direct contact with the ground, it is advisable to use impregnation to increase durability.
Larch is an excellent choice for a wide range of construction applications due to its exceptional physical properties and aesthetics.
INFLUENCE OF TEMPERATURE ON LARCH LUMBER?
The effect of temperature on larch lumber is a key factor in its drying and processing. Temperature affects both the physical and chemical properties of the wood, which has a direct impact on its quality and durability.
Physical properties and drying
Temperature and humidity : When drying larch lumber, it is important to monitor both temperature and relative humidity. High temperatures (20-30°C) combined with humidity around 25% can make the wood susceptible to blue stain, a process where unsightly spots appear on the surface of the wood, often caused by fungi.
Wood should be stored with sufficient gaps to ensure good air circulation, which helps to speed up the drying process and minimize the risk of condensation.
Air circulation : The effect of temperature on air circulation is also essential. During natural drying, air moves both horizontally and vertically, which affects the rate of evaporation of water from the wood surface. In the summer months, it is recommended to provide shading for the wood against direct sunlight, which can cause invisible cracks and reduce the mechanical properties of the wood.
Chemical properties and resistance
Natural resistance : Larch, especially Siberian larch, exhibits high resistance to rot and insect damage due to the content of resins. These chemicals protect the wood from microbial degradation and slow down the decomposition processes
The cold and dry conditions in which Siberian larch grows further contribute to its longevity and preservation of structure.
Temperature extremes : Sudden changes in temperature can accelerate the aging of wood and lead to cracking or warping. In addition, acidic environments can change the appearance of wood and cause unsightly stains.
Therefore, it is important to protect larch lumber from extreme weather conditions.
Temperature has a major impact on larch lumber at various stages of its processing. Proper control of temperature conditions during drying and protection from extreme temperatures are key to maintaining the quality and durability of larch wood.
WHAT IS THE LARCH LIMBER DRYING PROCESS?
Larch drying methods
Natural drying
Wood is exposed to natural conditions such as sun and wind. Fresh lumber is usually stored in the air, which can last from a few months to a few years, depending on the type of wood and climatic conditions.
Advantages : Low cost and minimal equipment required.
Disadvantages : Long drying time and risk of wood damage (e.g. by fungi) due to weather variability
Artificial drying
This process involves the use of hot air kilns, where the wood is dried using controlled air circulation and elevated temperatures. This method can achieve lower moisture content than natural drying.
Artificial drying phase :
Heating : Temperatures below 100°C for water condensation on the surface of the wood.
First drying phase : Rapid drying of the surface at 100°C.
Second phase : Increasing the temperature to 130 °C for the wood core.
Final drying : Maintaining the temperature around 100 °C to stabilize the humidity
Advantages : Speed and control over the process.
Disadvantages : Higher equipment and energy costs, risk of wood deformation during rapid moisture reduction
Consequences of insufficient drying
Cracks along the grain that occur on the leading edge of the wood.
Board deformation (e.g. bowing or “propeller”).
Reduced strength and durability of building elements
Drying larch is a key step in preparing wood for construction purposes. A properly executed drying process ensures the longevity and stability of the wood, which is essential for its use in structures and interiors.
Send us a quick request
you can also find us at:

